Customized Stainless Steel Solutions: Plasma and Oxy Profile Cutting at K999 Engineering & Construction Workshop
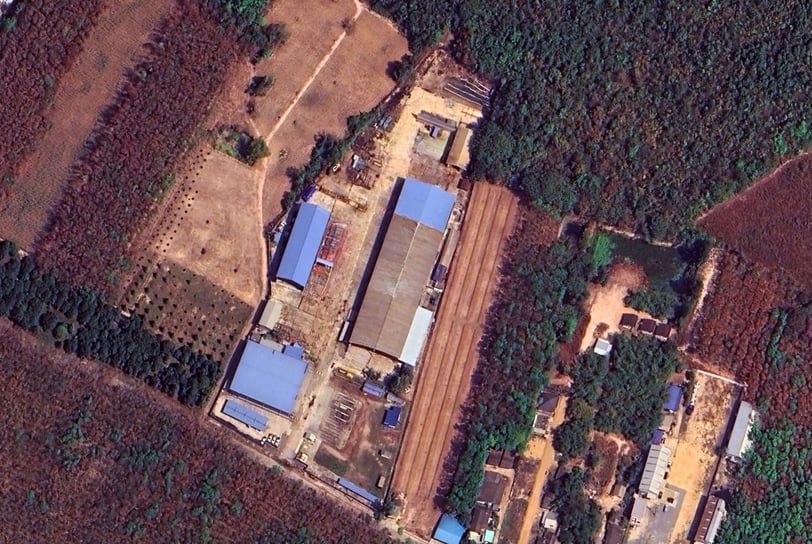
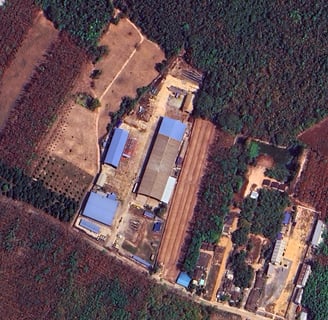
Introduction to K999 Engineering & Construction Workshop
K999 Engineering & Construction Workshop stands as a leading entity in the industry, renowned for its unwavering commitment to delivering high-quality stainless steel solutions. Established with the mission of providing exceptional engineering and construction services, K999 has cultivated a reputation over the years founded on expertise, innovation, and precision. The workshop leverages state-of-the-art technology, ensuring that each project meets the highest standards of excellence.
With a specialized focus on stainless steel fabrication, K999 Engineering & Construction Workshop has honed its skills in various areas of engineering, particularly in cutting-edge profile cutting services, including plasma and oxy-fuel methods. The workshop’s team of skilled professionals possesses extensive knowledge and experience, enabling them to tackle complex projects with ease and efficiency. Their understanding of industry demands and dedication to continuous improvement positions them as a key player in the stainless steel market.
K999 Engineering & Construction Workshop utilizes advanced technologies to enhance the quality of their offerings. The incorporation of precision machinery and innovative processes allows for the creation of tailored solutions that meet specific client requirements. By embracing modern techniques, the workshop ensures optimal efficiency while maintaining a focus on sustainable practices. This alignment with contemporary advancements in engineering demonstrates K999’s commitment to not only meeting but exceeding client expectations.
Ultimately, this introduction lays the groundwork for a deeper understanding of the extensive services provided by K999 Engineering & Construction Workshop. As we delve into their specific capabilities, such as profile cutting solutions, we will uncover how their dedication to quality and technology aligns with the needs of the modern marketplace, solidifying their position in the competitive landscape of stainless steel fabrication.
Understanding Plasma and Oxy Profile Cutting Technology
Plasma and oxy profile cutting are two pivotal technologies employed in the fabrication of stainless steel components at K999 Engineering & Construction Workshop. These methods are distinguished by their mechanisms and material compatibilities, making each suited for specific applications.
Plasma cutting utilizes a high-velocity jet of ionized gas, or plasma, to achieve cutting. The process begins with a gas being energized electrically to create plasma, which reaches temperatures exceeding 20,000 degrees Celsius. This intense heat enables the plasma cutter to melt stainless steel and other conductive materials effectively. The precision of plasma cutting is particularly noteworthy; it can achieve intricate designs with minimal kerf, resulting in a cleaner edge and reduced finishing work.
On the other hand, oxy-fuel cutting relies on the combustion of gas—typically acetylene or propane—with oxygen to create a flame that can melt metal. This method is not only effective for thicker plates but also offers greater versatility in terms of the types of materials it can cut, including carbon steel and some non-ferrous metals. While not as precise as plasma cutting, oxy-fuel cutting is advantageous in applications that prioritize speed over detail, providing significant productivity benefits.
Each method presents distinct advantages. Plasma cutting excels in speed and precision, making it preferable for detailed stainless steel components, while oxy-fuel cutting is more economical for thicker materials and simpler cuts. The choice between these cutting technologies ultimately depends on the specific requirements of the job, such as material thickness, complexity of the cuts, and desired finish.
In essence, plasma and oxy profile cutting technologies represent the forefront of modern metal processing, offering efficiency, versatility, and precision in the fabrication of stainless steel and quenched and tempered plates at K999 Engineering & Construction Workshop.
Custom Solutions Based on Customer Supplied Drawings
K999 Engineering & Construction Workshop stands at the forefront of providing customized stainless steel solutions through its adept plasma and oxy profile cutting services. A fundamental aspect of these tailor-made offerings lies in the ability to utilize customer-supplied drawings. This not only allows for precision in cutting but also ensures that the specifications reflect the unique needs of each client. The collaborative process begins with the submission of detailed technical drawings by customers, which may include precise dimensions, design features, and material specifications.
Upon receipt of these drawings, the skilled engineers at K999 engage in a thorough interpretation phase. This involves assessing the feasibility of the design, evaluating materials, and determining the most efficient cutting methods, whether it involves plasma or oxy cutting technologies. Engineers utilize advanced software to create detailed plans that pave the way for the later stages of production. This collaborative approach is vital as it allows customers to clarify their concepts, ensuring a shared understanding of the final product.
The industries served by K999 are diverse, ranging from construction and manufacturing to automotive and aerospace. Each project underscores the workshop's commitment to delivering precise, high-quality results tailored to specific applications. For instance, a recent collaboration with a construction firm required the intricate cutting of steel beams to fit a bespoke architectural design. The successful execution of such projects not only highlights K999's capabilities but also demonstrates its ability to adapt to the multifaceted requirements of various sectors.
Ultimately, the engagement between K999’s engineers and clients cultivates a pathway towards achieving custom solutions that fulfill design aspirations and operational needs. This approach reaffirms the workshop's dedication to precision and quality, ensuring that every finished product aligns perfectly with customer expectations.
Quality Assurance and Final Product Delivery
At K999 Engineering & Construction Workshop, ensuring the highest quality of customized stainless steel Australia solutions is a fundamental priority. The workshop employs rigorous quality assurance measures throughout the manufacturing process to guarantee that each product adheres to both industry standards and specific customer requirements. This commitment to quality is embedded in every project, from initial design to final delivery.
A comprehensive inspection process is implemented at various stages of production. This involves meticulous visual inspections and the use of advanced measuring equipment to verify dimensions and tolerances. The workshop adheres to established industry standards such as ISO 9001, which provides a framework for consistent quality management. These standards ensure that all products not only meet strict safety protocols but also maintain structural integrity, which is critical in applications where strength and durability are paramount.
Testing for structural integrity is another crucial component of K999 Engineering’s quality assurance strategy. Each customized stainless steel piece undergoes rigorous testing procedures, which may include non-destructive testing methods. These tests evaluate the material's performance under different conditions, ensuring that it can withstand the operational demands it is designed for. By employing such thorough testing methods, K999 Engineering reinforces its dedication to delivering solutions that clients can rely on.
Besides quality assurance, the logistics of product delivery are also a key factor in customer satisfaction. K999 Engineering & Construction Workshop prioritizes timely and reliable service by implementing an efficient delivery system. Once the quality control checks have been completed, the finished products are meticulously packaged to prevent any damage during transit. The company collaborates with experienced logistics partners to ensure that the delivery schedules align with customer expectations, reinforcing the notion that high-quality cutting solutions come with reliable service.